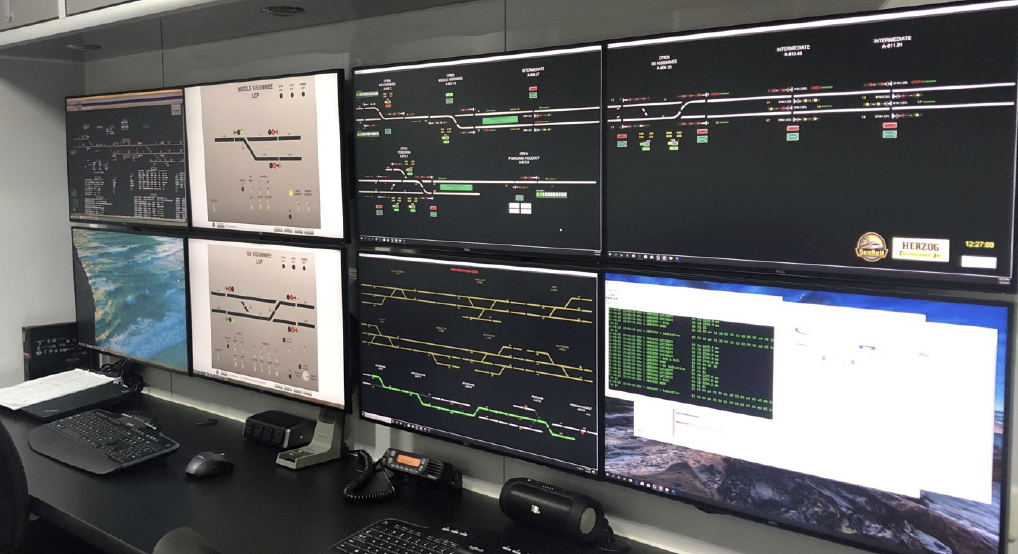
CHALLENGE
Before the introduction of the new Signal Testing System, testing and commissioning railway signal systems were labor-intensive and error-prone. Several signal personnel were required to be present in the field during the cutover phase to manipulate signal inputs and outputs, making it a time-consuming and costly process. Testing engineers often had limited visibility of the overall control system, leading to potential errors and delays in the cutover process.
SOLUTION
FrameworX by Tatsoft was selected as the platform to build the Signal Testing System due to its flexible, real-time capabilities. The system was designed to allow remote manipulation of signal systems from a centrally located mobile command center (Cutover Trailer), eliminating the need for on-site personnel at multiple field locations during signal system testing. The two main components of the system are:
- Wayside System Simulator (WSS): This device simulates real-world signal behaviors such as the movement of trains, switch operations, and signal responses. It collects input from the field and sends it to the mobile command center.
- Mobile Command Center (Cutover Trailer): Equipped with an HMI (Human-Machine Interface) powered by FrameworX, this centralized unit allows engineers to remotely control and test signals without requiring personnel at the field location.
RESULTS
The Signal Testing System, built using FrameworX by Tatsoft, has revolutionized how Herzog tests and commissions railway signal systems. By leveraging remote manipulation and centralized control, the system has:
- Reduced field personnel requirements by over 60%.
- Increased the accuracy of tests and reduced human error.
- Minimized testing time by up to 70% in some cases.
- Reduced costs related to overtime, lodging, and other logistical overhead. • Improved safety by limiting the exposure of personnel to the field environment.